
Cold Plates
Battery Cooling Technology on a Platter

RIGID
UNIFORM
At Alkraft, driving change and progress through thermal innovation has been a fundamental tenet of our existence right from our founding over three decades ago. Now, as the pace of change is accelerating faster than it ever has, we are once again at the forefront, enabling and driving change with cutting-edge Thermal Management Solutions for electric, diesel and alternative fuel applications across a wide range of industrial segments.
Precision Designed & Engineered for Surface Flatness, Structural Rigidity, and Temperature Uniformity throughout the Surface Area of the Cold Plate.
Alkraft’s range of Cold Plates cover a wide variety of technologies, designs and application areas. We have Cold Plates for Electric Vehicles of various sizes, for fast charging stations, and for renewable energy storage applications. The high sensitivity of Lithium Ion batteries towards temperature extremities makes Cold Plates a crucial component for battery thermal management.
A key aspect of our cold plate design process involves the optimization of their internal flow paths, achieved through iterative Computational Fluid Dynamics (CFD) simulations. This meticulous design approach ensures that coolant flow is maximized for efficient heat removal from the battery cells.
The surface flatness of Alkraft’s Cold Plates is engineered to ensure maximum surface contact with the battery cells. This precision engineering is critical for enhancing thermal transfer efficiency, allowing for more effective cooling across the entire surface of the battery. Structural rigidity is another cornerstone of Alkraft’s cold plate design given its role in supporting the battery’s weight. Our Cold Plates are developed using advanced CAE techniques that enable us to optimize their strength and weight, ensuring they can support the battery without compromising the system’s overall weight efficiency.
Temperature uniformity across the Cold Plate’s surface is another critical performance metric. Alkraft’s Cold Plates are designed to provide consistent cooling, ensuring temperature uniformity throughout the battery surface. This uniform cooling is essential for maintaining battery efficiency and longevity, preventing hot spots that could degrade battery performance over time.
Alkraft’s expertise in heat transfer product design together with our use of advanced design and manufacturing process technologies make our Cold Plates the preferred choice for OEMs for their thermal performance, structural integrity, and durability.
At Alkraft, driving change and progress through thermal innovation has been a fundamental tenet of our existence right from our founding over three decades ago. Now, as the pace of change is accelerating faster than it ever has, we are once again at the forefront, enabling and driving change with cutting-edge Thermal Management Solutions for electric, diesel and alternative fuel applications across a wide range of industrial segments.
Cold Plate Core Construction
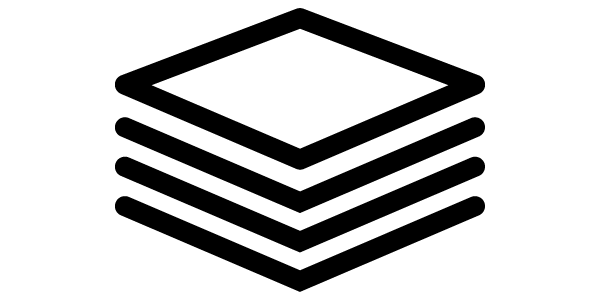
Stacked
Cold Plates
1000 x 900mm
Fast Charging Applications,
and Renewable Energy Storage

Inner Fin
Cold Plates
1000 x 900mm
Fast Charging Applications,
and Renewable Energy Storage

Extrusion
Cold Plates

Stamped
Cold Plates
1000 x 900mm
Case Studies